中金 | 一體壓鑄:減重降本驅動 行業放量將至
原標題 中金 | 一體壓鑄:減重降本驅動,行業放量將至
來源 中金點睛
文 厙靜蘭 陳顯帆等
我們認爲,一體化壓鑄技術具備減自重、提升生產效率、降低生產成本的優勢,伴隨特斯拉、多家新勢力逐步應用,一體化壓鑄在新能源汽車上的應用已成爲較爲明確的趨勢。我們認爲產業鏈各個環節均有望受益,我們從設備端、材料端、製造端三個方向提示投資者關注賽道投資機會。
摘要
車身技術的革新始終以兼顧安全性的同時降低車重爲核心,已經歷結構簡化、材料替換兩個階段。汽車工業發展初期,主要採用非承載式車身結構,隨設計工藝進步、規模效應降低成本,結構更簡單、質量更輕、燃油經濟性更好的承載式車身在20世紀50年代後逐步成爲SUV、轎車車身設計的主流選擇。而在新能源化過程中,由於電池本身重量較大影響續航里程,而通過鋁替代鋼降低自重的成本低於增加電池以延長續航的成本,因此汽車輕量化的進程得以持續加速。
減重降本優勢驅動一體化壓鑄滲透率提升,CTC或成更遠期方向。傳統車身製造工序焊接點位較多,流程複雜,一體化壓鑄能夠實現部分或整體車身構件一體化成型,減少分體衝壓、壓鑄後焊接的複雜過程,具備效率高、成本低優勢,根據特斯拉的測算,後底板的一體化壓鑄可使得對應部件製造成本下降40%。而在一體化壓鑄技術持續發展過程中,汽車行業對於電池的結構簡化以及減重也產生新的追求,CTC技術應運而生,CTC技術取締了模組、電池包,將電芯直接集成至底盤,在減重、優化車身佈置方面具備較強優勢,當前特斯拉、零跑等整車廠已提出CTC架構,我們認爲CTC技術或成爲未來純電車身及底盤架構發展的重要方向。
一體壓鑄行業空間廣闊,進入壁壘較高,壓鑄廠相對整車廠更具規模優勢及技術積累,有望佔據較大市場份額。我們預計,2025年中國一體化壓鑄製造端、材料端市場規模有望達到178億元、88億元,2021-2025年CAGR均超過150%;設備端來看,2025年全球6000t及以上壓鑄機行業規模有望達47.2億元,2021-2025年CAGR爲96%。從壁壘來看,我們認爲一體化壓鑄存在設備領先性佈局、材料配比、模具設計等三大壁壘,進入門檻較高,競爭格局有望優於傳統壓鑄件。從參與者來看,整車廠、供應商均積極佈局,我們認爲,整車廠與第三方壓鑄廠共存的競爭格局將持續,但第三方壓鑄廠更具成本與技術優勢,有望佔據較大市場份額。
風險
一體化壓鑄滲透不及預期,行業競爭加劇。
正文
車身技術:非承載式到承載式,新能源加快輕量化進程
階段一:基於設計難度、製造成本考慮,非承載式車身曾是主流
非承載式車身是車身設計的早期主流技術路徑,設計簡單、易於組裝,但重量較大,且經濟型、舒適性較差。非承載式車身是一種將車身、底盤系統裝置於車架之上的底盤形式。非承載式車身能夠以統一的底盤配置不同類型的車身,具有易於組裝、維修的特點,並可以減少開發多款不同車型的設計成本與耗時,因此被廣泛應用於20世紀初期的汽車生產流水線。因非承載式車身裝配有較笨重的車架,導致其具有重量大、燃油經濟性差、重心高、空間利用率低、舒適性差的缺點。
圖表:非承載式車身特點

資料來源:搜狐汽車,中金公司研究部
非承載式車身適用於載重、非城市道路場景,部分車型仍有應用。由於車架、車身分置的結構能夠給予更大的緩衝空間,給予車身更大抗形變、抗震能力,更適應於非城市道路的顛簸路面,因此部分越野SUV、皮卡、載重商用車、等依舊採用非承載式車身架構。長城汽車、北京越野等均推出曾基於非承載式車身加購的中大型SUV,定位越野愛好者。
圖表:非承載式車型

資料來源:汽車之家,中金公司研究部
階段二:設計水平取得突破,規模效應降低成本,承載式車身成爲轎車、SUV的主流方案
伴隨設計工藝進步,規模效應降低成本,承載式車身逐漸成爲主流。承載式架構取消了剛性車架,將發動機、前後懸架等裝配於車身。與非承載式架構相比,承載式車身對材料強度及結構設計具有較高要求,模具成本也較高,因此直至20世紀30年代才逐步投入使用。1934年雪鐵龍推出第一款採用承載式車身的車型Traction Avant,該車型車身重心下降且更爲舒適,通用、克萊斯勒等亦紛紛效仿,陸續推出承載式架構車型。在設計技術不斷進步、規模效應逐步攤薄成本的作用下,承載式車身製造工藝得以普及,20世紀60年代末,乘用轎車普遍切換爲更爲輕便的承載式車身架構。
圖表:承載式車身特點

資料來源:General Motors官網,Road & Track官網,中金公司研究部
承載式車身適用於城市道路,自重較輕、舒適度高,逐步成爲SUV、轎車的主流選擇。承載式車身具有較多優點:承載式架構使車輛重心更低,帶來更好操控性能與舒適性;取消車架,減輕了整車質量,提高燃油經濟性;將底盤和車身融爲一體,提升了空間利用率。因此,承載式車身成爲轎車及城市型SUV主流選擇。
圖表:承載式車身特點

資料來源:搜狐汽車,中金公司研究部
階段三:新能源車裏程焦慮仍存,輕量化趨勢逐漸明晰
新能源車裏程焦慮仍存,輕量化需求迫切。由於新能源車電池重量較大,新能源車整車質量一般較傳統燃油車重10%,進而影響續航里程,因此我們認爲,新能源汽車輕量化需求迫切。據《電動汽車車身結構輕量化研究》,若純電動汽車整車重量能降低10%,平均續航里程將增加5%-8%,汽車整車重量每減少100kg,百公里電耗可降低約7.5%。據《節能與新能源汽車技術路線圖》規劃,2020、2025及2030年汽車減重目標分別爲較2015年下降15%、20%、35%,汽車輕量化需求迫切。
圖表:輕量化材料比較
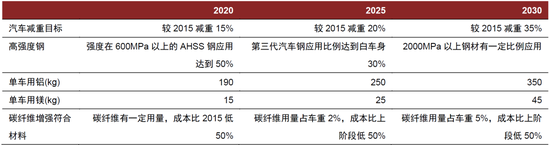
資料來源:工信部《節能與新能源汽車技術路線圖》,中金公司研究部
鋁合金綜合優勢凸顯,含鋁車身成爲重要選擇。傳統車身重量約佔汽車總重的30%,車身輕量化對整車輕量化意義凸顯。與鎂合金、碳纖維相比,鋁合金在密度、強度、成本與工藝難度上具有綜合優勢,能夠滿足輕量化、保證車身強度要求,因此含鋁車身爲輕量化重要選擇。具體來看,奧迪A8採用全鋁車身框架,與鋼製車身相比質量減輕30-50%,本田Insight Hybird轎車車身採用純鋁車身,較鋼製車身減重約40%,均起到較好輕量化效果。據國際鋁協估計,2020年我國純電車單車用鋁量爲173kg,而工信部發布的《節能與新能源汽車技術路線圖》規劃2025年、2030年單車用鋁量應分別超過250kg、350kg,單車用鋁仍有較大提升空間。
圖表:我國乘用車單車用鋁量

資料來源:國際鋁協,CM Group,中金公司研究部
圖表:輕量化材料比較

資料來源:萬得資訊,熊自柳《新能源汽車及其輕量化技術發展現狀與趨勢》,中金公司研究部
與提升電池容量相比,採用鋁製車身爲提升續航更經濟選擇。我們認爲,相比採用提升電池容量的方法,使用鋁替代鋼降低車身自重以延長續航更具有成本優勢。以特斯拉Model Y磷酸鐵鋰電池60kWh爲例,假設純電動汽車整車重量能降低10%,平均續航里程將增加8%,而鋁替代鋼材實際可達到接近40%的減重效果,我們測算若通過鋁替代鋼實現整車減重,同時保證續航里程不變,若以鋁替代鋼製車身,則對應有望節省成本超過1.2萬元。
圖表:全鋁車身較提升電池容量節約成本測算

資料來源:特斯拉官網,中金公司研究部
圖表:鋁車身較提升電池容量節約成本敏感性測算

資料來源:萬得資訊,中金公司研究部
降本優勢驅動一體化壓鑄滲透,CTC或成更遠期方向
傳統車身工藝製造工序複雜,一體化壓鑄具備效率高、成本低的優勢
傳統車身結構零部件較多,焊接等製造工序複雜,一體化壓鑄可實現提升生產效率的作用。傳統車身製造工序先通過沖壓、擠壓、鑄造完成各零部件生產,再使用焊接、鉚接工藝將零部件進行連接。傳統白車身由300-500個零部件構成,焊接點位可達4000-6000個。由於零部件衆多會導致尺寸誤差,因此汽車總裝出廠前需要進行近6個月總計三輪(MB1、MB2、MB3)匹配調試。而一體化壓鑄則可以通過將多個零件合併爲一個,簡化生產流程,並將調試時間縮減爲1-2輪,有效降低產線的資本投入以及提升生產效率。
圖表:傳統白車身架構
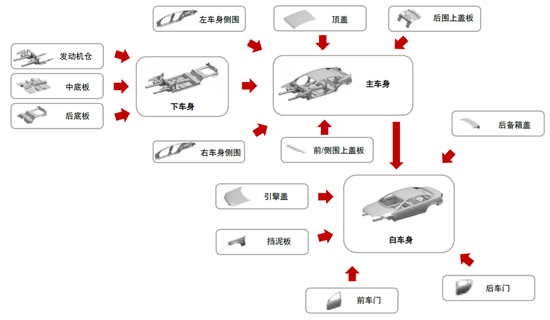
資料來源:北斗株式會社公司官網,中金公司研究部
圖表:傳統整車製造工藝流程

資料來源:中金公司研究部
受益於壓鑄機設備噸位提升,車身壓鑄件向大型化、集成化發展,讓一體化壓鑄成爲可能。隨壓鑄機鎖模力不斷提升,以及壓鑄材料與工藝的不斷完善,車身壓鑄件向大型化與集成化發展。車門框、A柱、後縱架、尾箱蓋等大型車身構件可通過4000T壓鑄機制造。以奧迪A8爲例,其減震塔鋁壓鑄件可替代原本由10個零件焊接而成的鋼製減震塔,實現減重10.8kg。特斯拉在美國、上海以及柏林工廠部署多臺6,000T噸位大型壓鑄機,實現了Model Y車型後底板一體壓鑄成型,未來引入更大壓鑄機後,我們認爲特斯拉有望實現一體壓鑄更大體積零件。以壓鑄機領先廠商力勁的大型冷室壓鑄機參數爲例,隨壓鑄機噸位上升,壓鑄機最大射料量也增加,實現壓鑄成型零件也越大。
圖表:我國臥式壓鑄機研製生產能力變化表

資料來源:《中國壓鑄行業發展歷程及現狀》,中金公司研究部;注:包含力勁子公司意德拉
圖表:壓鑄機鋁材最大射料量和壓鑄機噸位關係

資料來源:力勁產品宣傳手冊,中金公司研究部
圖表:壓鑄機噸位提升使更大壓鑄件成爲可能

資料來源:布勒公司,中金公司研究部
製造工藝流程簡化,實現生產提效降本。一體化壓鑄能夠實現部分或整體車身構件一體化成型,減少分體衝壓、壓鑄後焊接的複雜過程,簡化製造工序。以特斯拉工廠爲例,其通過傳統工藝製造的Model 3後底板有70個零部件,而後底板一體化鑄造的Model Y僅需兩個零部件,焊接點位從700-800個減少至50個。簡化後的流程工藝能夠顯著提升生產效率,特斯拉Model Y採用下底板一體化壓鑄後,對應部位製造時間由傳統工藝的1-2小時縮減至3-5分鐘。相較傳統衝壓-焊接工藝,壓鑄件材料利用率更高,且可實現一臺壓鑄機代替多條成型與組裝生產線,從而大大減少人員、土地成本。
圖表:特斯拉Model 3與Model Y後車身比較

資料來源:特斯拉官網,中金公司研究部
圖表:特斯拉一體化壓鑄工藝提效降本

資料來源:特斯拉官網,中金公司研究部
更新一輪車身及底盤設計革命:CTC
以減重降本爲目的,CTP已初步應用,CTC落地在即。傳統電池系統結構採用“電池+模組+電池包”結構,具電池佔用面積大的缺陷。爲使有限汽車空間搭載更多電池,寧德時代等廠商推出CTP架構,將電芯集成至電池包,該技術已應用至特斯拉Model 3,蔚來ES6等車型。CTC則是一種將電芯裝直接配置至車輛平臺的電池底盤一體化技術,CTC技術直接取消了模組,將電芯集成在底盤,電芯既是電量的載體,也是車身結構件的一部分,參與碰撞受力。CTC方案進一步提升集成度與空間利用率、減少了零部件數量,實現更優的空間佈局。
圖表:三代電池底盤技術比較

資料來源:第一電動公衆號,中金公司研究部
當前主要的CTC方案分爲兩類:
►方案一:將底板面板與電池包上殼體合二爲一,集成於電池,中底板爲電池殼體所替代。電池上蓋與門檻及前後橫樑形成的平整密封面通過密封膠密封乘員艙,底部通過安裝點與車身組裝。該方案將電池包作爲一個整體與車身集成,密封及防水性能較好,但由於缺少傳統電池包上蓋,改用車身+下蓋負責密封,對乘員艙熱管理的設計要求較高。
►方案二:底板面板與電池包上殼體合二爲一,集成於車身,將電池包的結構分爲上殼體和電池本體兩個部分。通過密封膠實現車身與電池本體的密封,底部通過安裝點與車身組裝。該方案具有一定密封難度,需要爲氣密性開發檢測線與返修線,增加成本與工時。
CTC在減重、優化車身佈置方面具備較強優勢,但同時對於密封性、熱管理的要求相應提升。由於CTC方案將電池盒上蓋與車身中底板的部分零部件進行了集成處理,電池盒與車身連接後需要通過密封膠實現密封,由此對於密封的要求較此前有中底板的方案將有所提升。另外,由於取消了電池包和模組的結構,其安全性和穩定性將受到挑戰,對電池系統的溫度一致性要求更高,熱管理的重要性將進一步提升。
圖表:國內外企業CTC技術佈局進展

資料來源:各公司官網,網易網,中金公司研究部
特斯拉:CTC架構計劃於Model Y上實現,德州工廠率先佈局
特斯拉於2020年電池日提出了其CTC架構,計劃將應用於其Model Y上。特斯拉以電池上蓋取代原有座艙地板,將電池包上殼體直接連接在座椅等構件上,直接作爲乘員座艙地板。特斯拉在電池包殼體上焊接四根橫樑用於安裝前排座椅,使其電池上蓋能夠同時起車身地板、封裝電池作用。
根據特斯拉的測算,該承載式車身路線將能夠將電池組集成於車身結構中,配合一體化壓鑄,可節省370個零部件,車身減重10%,每kWh電池成本降低7%。特斯拉計劃2022年於德州超級工廠搭配4680電池實現Model Y上CTC底盤結構的組裝。
圖表:特斯拉CTC結構將電池上殼體用作座艙地板
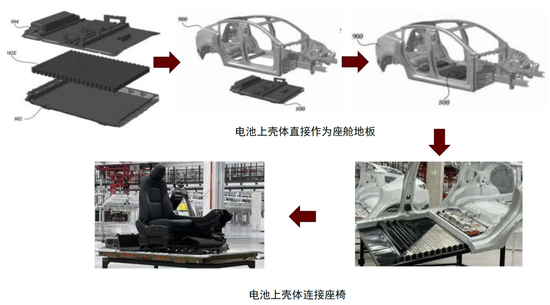
資料來源:特斯拉官網,中金公司研究部
零跑:利用雙骨架環形梁式結構,計劃於零跑C01上投入使用
零跑於2022年3月對外公佈了其智能動力CTC電池底盤一體化技術,並將於其中大型轎車零跑C01上投入使用。零跑CTC線路實現電池與底盤、下車身集成耦合,使得電池佈局空間增加14.5%,續航提升10%,整車扭轉剛度提升25%,車身重量降低15kg。
零跑利用雙骨架環形梁式結構,將結構梁與電池托盤形成多個環形結構,能夠有效固定電池組,利用車身縱梁、橫樑形成完整的密封結構。其雙骨架環形梁式結構能夠有效提高結構強度,增加密封性與安全性。
圖表:零跑汽車雙骨架環形梁式結構
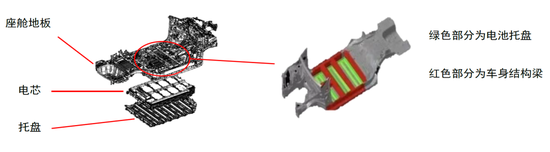
資料來源:太平洋汽車網,中金公司研究部
比亞迪:電池上殼體代替部分中底板,計劃於海豹上投入使用
比亞迪在2021年9月對外展示了其基於純電e3.0平臺打造的全新概念車ocean-X,並宣佈該平臺採用了比亞迪開發的CTB車身電池一體化技術。比亞迪計劃在其2022年發售的新車型海豹上採用e3.0平臺,該車型包括後驅版(550km+150kW)、後驅長續航版(700km+150kW)、四驅版(650km+390kW)。比亞迪海豹用電池上殼體代替部分中底板,電池上蓋與門檻及前後橫樑形成平整密封面,通過密封膠密封乘員艙,底部通過安裝點與車身組裝,有望進一步提升其電池容量與空間利用率。
一體壓鑄行業空間廣闊,設備+材料+工藝構築三大壁壘
2025年中國一體化壓鑄產品市場規模有望達到近200億元。
一體化壓鑄件單車重量可達180kg,對應ASP接近萬元。當前一體化壓鑄主要的應用領域是前、後底板以及電池盒。從重量上看,按照集成輪罩的方案,我們預計前底板+後底板+電池盒整體重量可達180kg。按照一體化壓鑄件50元/kg的售價進行估算,我們認爲,一體化壓鑄對應單車可配套價值量最高可達9000元。
圖表:一體化壓鑄單車價值量較高

資料來源:中金公司研究部
主要應用於B級及以上新能源純電車型,後底板、前底板已實現量產,電池盒仍處研發階段。我們認爲,一體化壓鑄具備減自重、提高生產效率、延長續航的優勢,而當前B級及以上的新能源車裏程焦慮較爲突出,因此我們認爲應用於減重需求較大的B級及以上純電車型以及定位高端的部分A級車。當前一體化壓鑄後底板已率先被特斯拉量產,而前底板也已有部分供應商獲得定點,電池盒則由於體積較大,壓鑄技術當前還在研發階段,目前主要是擠出+焊接路線。
我們預計後底板滲透率有望率先提升,電池盒後續滲透率提升預期較高,前底板滲透率預期則較爲保守。向前看,我們認爲,後底板碰撞風險較小,已有多個主機廠、零部件廠商成功試製及量產,因此滲透率有望率先提升;電池盒方面,一體化壓鑄相對於擠出+焊接路線具備較強的成本優勢,因此我們認爲高壓壓鑄電池盒技術一旦突破,滲透率有望迅速提升;而前底板則考慮到有相對較高的碰撞風險而滲透率提升較慢。總體來看,我們預計2025年前底板、後底板、電池盒滲透率分別有望達到15%、31%、35%。
圖表:新能源乘用車一體化壓鑄滲透率預測

資料來源:乘聯會,中金公司研究部
我們對於材料端、設備端、製造端的行業空間分別進行了測算:
►材料端:根據我們的產業鏈調研,當前部分車企應用的後底板一體化壓鑄未集成輪罩,因此單件重量較低,後續技術逐步成熟,集成度提升,我們預計單件重量有望達到60kg。免熱合金單價方面,我們假設鋁價保持在20000元/噸左右,原材料供應商的加工費約爲5000元/噸,對應單噸價格約爲25000元。而伴隨生產規模逐步擴大,新進入廠商增加,免熱合金材料單價有望逐步下降。我們預計2025年中國免熱合金市場規模有望達到88億元,較2021年CAGR達到155%。
圖表:一體化壓鑄材料端行業規模

資料來源:中汽協,乘聯會,中金公司研究部
►設備端:考慮到壓鑄機設備面向全球市場進行銷售,我們估算全球市場6000噸以上超大型壓鑄機市場空間。我們假設下游購買設備僅用於新增新能源汽車產能,產能利用率70%,單個設備年產壓鑄件約8萬件,一臺大型壓鑄機+壓鑄島等配套設備價值量平均約0.5-0.6億元。此外,考慮到產業發展前期,下游客戶對於配套新車型的超大型壓鑄件,需要經過進行1年以上的驗證期,因此部分設備採購及確認收入預計將早於實際部件上車,我們粗略估計該週期爲半年左右。中性假設下,我們預計2025年全球6000噸以上超大型壓鑄機對應市場空間有望達到47.2億元,較2021年CAGR達到96.0%。
圖表:全球超大型壓鑄機銷量預測

資料來源:中汽協,Marklines,中金公司研究部
圖表:全球超大型壓鑄機市場空間預測

資料來源:中汽協,Marklines,中金公司研究部
►製造端:根據我們當前的產業鏈調研以及鋁壓鑄廠商成本加成規律,我們預計成品一體化壓鑄產品單價約爲50元/kg,後續伴隨良品率、產能利用率提升,單價有望逐步下降。我們預計2025年國內一體化壓鑄製造端行業規模有望達到179億元,較2021年CAGR達到156%。
圖表:一體化壓鑄製造端行業規模預測

資料來源:中金公司研究部
設備+材料+工藝構築三大壁壘
設備端:大型壓鑄機供給有限,設備前瞻性佈局成爲競爭重點。當前具備6000t及以上壓鑄機生產能力的國內供應商僅力勁、海天金屬、伊之密,國外有意大利IDRA(已爲力勁收購)及瑞士布勒,設備供給有限。力勁科技當前最大噸位產品可達到1.2萬噸,當前力勁大型壓鑄機月產能在2-3臺;海外供應商主要爲布勒,布勒當前量產的最大噸位產品爲6000t,更大噸位的產品仍需一段時間。國內廠商海天金屬、伊之密也在積極佈局研發和生產。
圖表:國內外大型壓鑄設備產能(截止2022年4月)

資料來源:各公司官網,各公司公告,中金公司研究部
材料端:免熱處理合金爲一體化壓鑄最佳選擇。傳統壓鑄方式需要通過熱處理減少氣泡產生,但熱處理過程易造成變形與表面質量缺陷,降低壓鑄結構件精密性與機械性能。熱變形問題可以通過後續機械矯正等緩解,但這對生產效率、生產成本會產生較大影響。隨壓鑄結構件尺寸和複雜性增加,熱變形問題愈發顯著,免熱處理材料不可或缺。
免熱合金行業參與者較爲有限,進入壁壘不斷提高。當前擁有免熱處理合金專利的廠商包括海外的美國鋁業、德國萊茵菲爾德,以及國內的立中集團、上交大丁院士團隊、廣東鴻圖等。我們認爲,免熱合金壁壘較高,主要體現在:1)研發壁壘。免熱合金即向原材料鋁中加入一定比例的硅、鎂、鉬等金屬或非金屬元素,在某個特定的、較窄的比例區間內,纔可以使得鑄造鋁合金的性能達到免熱標準。需要企業投入較大的研發支出和人員,同時也需要多年的生產經驗積累。2)先發者通過專利提升行業進入壁壘。具備先發優勢的廠商通過專利中對於合金中其他元素添加的比例進行限制,使得後進入者越來越難以繞過原有專利研發出符合要求的產品。
圖表:熱處理可顯著提升材料性能表現
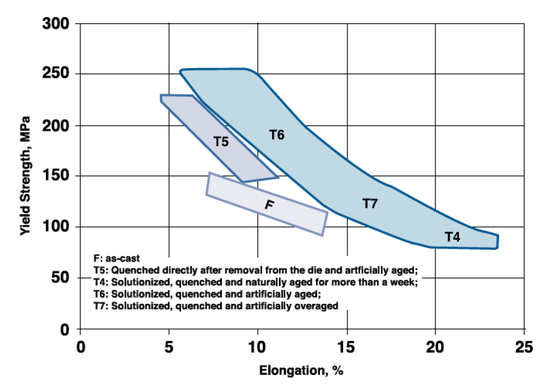
資料來源:Alcoa、中金公司研究部;注:F爲非熱處理,T4-T7爲不同熱處理方式
圖表:免熱處理合金專利儲備情況

資料來源:各公司產品手冊、國家知識產權局、WIPO、中金公司研究部
工藝端:大型一體化壓鑄工藝難度較大。爲實現大規模量產過程中保持高良率及大型部件的一致性,一體化壓鑄企業在工藝Know how需具有豐富積累。設計層面主要爲模具的設計,包含模具結構、型芯、冷鐵的配置。模具在設計過程中要考慮其排氣結構,該過程需不斷仿真模擬及生產實操,依賴於豐富設計經驗。部件成型層面,爲保證大型一體化零部件的精度、一致性,需要企業熟練掌握對壓鑄機壓射壓力及速度控制的配置,對鋁液溫度、流速、壓力配置精準把控,具有較高工藝難度。
多方積極佈局一體化壓鑄,車企自制、供應商模式有望共存
當前特斯拉、蔚來、小鵬等新能源車企積極佈局一體化壓鑄,同時大衆、沃爾沃等傳統車企也不斷探索一體化壓鑄。除整車廠外,國內第三方壓鑄廠也取得了較大進展。我們認爲,整車廠與第三方壓鑄廠共存的競爭格局將持續,但第三方壓鑄廠更具有成本與技術優勢。
整車廠:多車企對一體化壓鑄技術的優勢較爲認可,助力一體化壓鑄滲透率提升。
►特斯拉:特斯拉model Y後底板已實現一體化壓鑄。目前其上海工廠有3臺6000T壓鑄機,其美國加州及德克薩斯州工廠皆配置有大型壓鑄機。特斯拉已爲其新一代電動皮卡Cybertruck的生產訂購8000T壓鑄機,用於生產其一體化後底板。
►蔚來:蔚來於2021年10月宣佈其成功開發了免熱處理鋁合金以用於大型壓鑄件,其當年發佈的ET5後底板採用了一體化壓鑄設計。
►小鵬:小鵬武漢工廠除常規衝壓、焊接、塗裝車間,還引入了一體化壓鑄車間,計劃將引進一條以上超大型壓鑄島及自動化生產線。
►小米:據《壓鑄週刊》,小米汽車已與國內某主流品牌壓鑄機制造商簽約,向其採購一臺以上超大噸位壓鑄機,用於一體化壓鑄汽車零部件生產製造項目。
►大衆:據德國《商報》報道[1],大衆將於德國沃爾夫斯堡新建一座工廠用於生產新一代電動車Trinity,新工廠將引入一體化壓鑄技術,並於2026年起生產首批汽車,預計可實現10小時生產一臺整車。
►沃爾沃:沃爾沃將擴建其瑞典Torslanda工廠,計劃將於下一代全電動平臺上引入一體化鑄造工藝,規劃將於2025年實現量產。沃爾沃目標在後底板生產上使用8000T鎖模力壓鑄機,節拍在140s。
圖表:整車廠積極佈局一體化壓鑄

資料來源:搜狐汽車,財聯社,《壓鑄早報》,中金公司研究部
第三方壓鑄廠:更具成本與工藝優勢,多個廠商已試製成功並獲得定點
當前已有多個廠商獲得一體壓鑄訂單,並且試製成功。參與佈局一體化壓鑄的第三方壓鑄廠包括文燦股份、廣東鴻圖等具備車身結構件製造經驗的廠商,其他有輕量化業務生產經驗的拓普、愛柯迪、美利信等也有所佈局。當前,文燦股份、拓普股份、美利信目前已獲確定性定點,而廣東鴻圖已與下游客戶展開大型一體化壓鑄件試製合作。
我們認爲,第三方壓鑄廠更具規模效應及工藝優勢,有望在未來佔據較大市場份額。技術方面,汽車整車廠多采用衝壓+焊接傳統車身製造工藝,在壓鑄件領域佈局較少。而第三方壓鑄廠在壓鑄件製造領域具有長期技術及工藝積累,在模具開發、參數調試與實驗模擬上已形成成熟流程體系,工藝經驗積累深厚。成本方面,第三方壓鑄廠可實現不同品牌車型大型一體化構件的生產,能夠攤薄壓鑄島、廠房支出,形成規模效應,而整車廠車型較爲單一且銷量有限,自主生產一體化壓鑄件投入較大。我們認爲,第三方壓鑄廠具備成本與工藝優勢,其未來發展可期。
圖表:第三方壓鑄廠佈局一體化壓鑄情況(2022年5月)

資料來源:各公司公告,各公司官網,蓋世汽車,中金公司研究部
[1] https://new.qq.com/rain/a/20220301A0C92O00
文章來源
本文摘自:2022年5月17日已經發布的《一體壓鑄:減重降本驅動,行業放量將至》
厙靜蘭SAC 執證編號:S0080120080100
陳顯帆 SAC 執證編號:S0080521050004 SFC CE Ref:BRO897
鄧 學 SAC 執證編號:S0080521010008 SFC CE Ref:BJV008
齊 丁 SAC 執證編號:S0080521040002 SFC CE Ref:BRF842
張梓丁 SAC 執證編號:S0080517090002 SFC CE Ref:BSB840
李昕陽 SAC 執證編號:S0080121070352